From multi-material and multi-color printing to the creation of intricate metal parts, these developments have expanded the possibilities of what can be achieved with this innovative manufacturing process.
The realm of 3D printing has extended beyond trinkets and figurines, with the emergence of bioprinting and the potential to revolutionize healthcare. This is a basic overview of some of the notable trends and advancements in 3D printing technology.
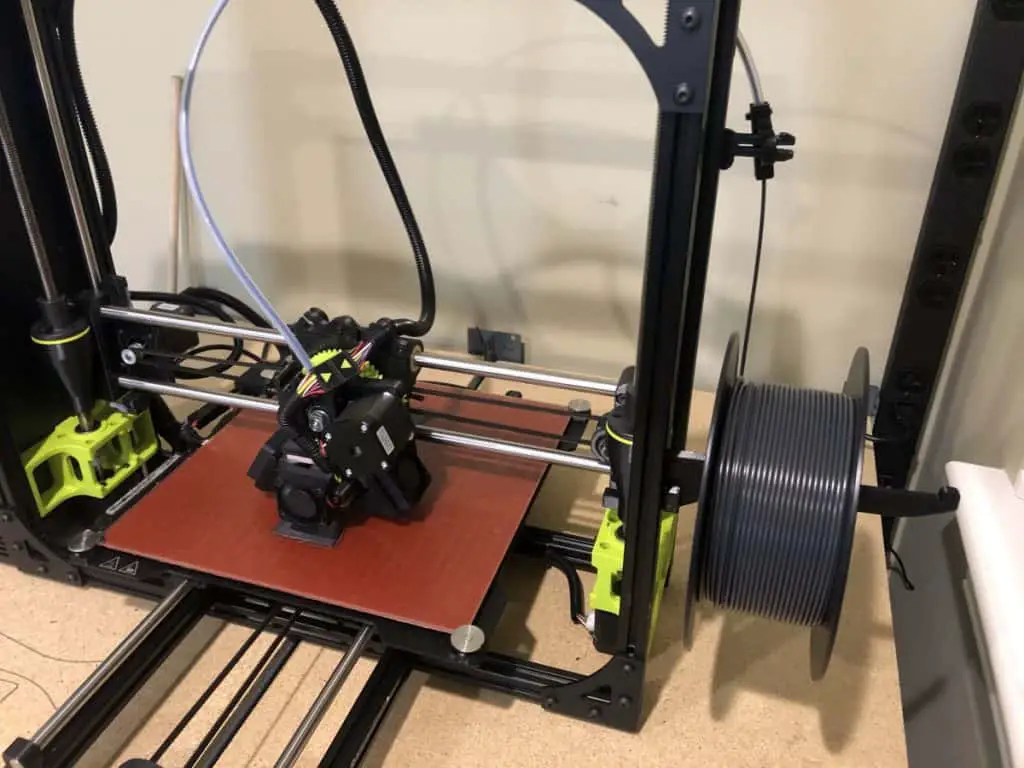
Multi-material and Multi-color Printing
Traditional 3D printers were limited to using a single material and color. However, recent advancements involve the simultaneous printing of multiple materials and colors within a single object. This allows people to create more complex and realistic models.
Dual Extrusion
One common method for multi-material printing is through the use of dual extrusion. The 3D printer is equipped with two or more extruders, each capable of depositing a different material.
As the object is being printed layer by layer, the printer can switch between extruders to deposit different materials. For example, one extruder may deposit a rigid plastic while the other extruder simultaneously deposits a flexible material. This allows for the creation of objects with distinct material properties.
Inkjet Technology
Some 3D printers utilize inkjet-based technology to achieve multi-color printing. Instead of using multiple extruders, they employ a single extruder or print head that contains multiple nozzles or channels for different colors. The printer deposits colored inks or pigments layer by layer, blending them to achieve the desired colors and patterns. By controlling the deposition of each color, intricate and colorful objects can be produced.
Material Mixing
Certain 3D printers enable the mixing of different materials to create unique composite materials or gradients. This is typically achieved through a single extruder that has the capability to blend or mix different materials together. For example, the printer can simultaneously feed two filaments containing different colors or materials into the extruder. The materials are then fused or blended during the printing process, resulting in a multi-colored or composite object.
Post-Processing and Assembly
Another approach to multi-material printing involves printing individual components or parts separately using different materials or colors and then assembling them after the printing process. This can be done by designing the object in such a way that it can be easily disassembled and reassembled. Each component can be printed using your desired material or color, and then the final object is assembled to create the multi-material or multi-color result.
Metal 3D Printing
Metal 3D printing has seen significant advancements. Techniques like selective laser melting (SLM) and electron beam melting (EBM) allow for the creation of complex metal parts with high precision and strength. Metal 3D printing is increasingly being used in the aerospace, automotive, and medical industries. Here are some examples.
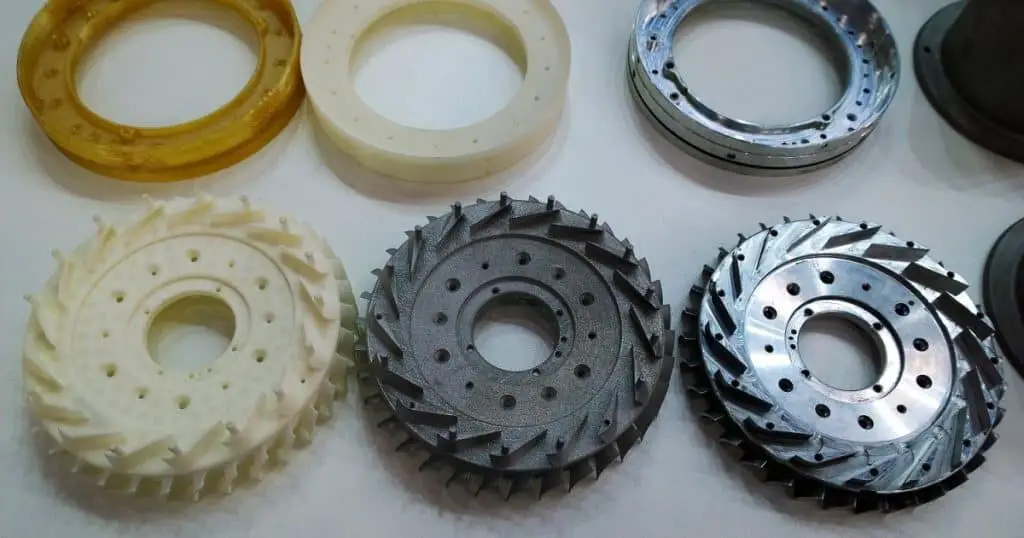
Aerospace Industry
Engine Components
Metal 3D printing is revolutionizing the production of engine components in the aerospace industry. Turbine blades, fuel nozzles, and combustion chambers can be 3D printed with extreme precision, improved performance, and reduced weight to enable engines to operate more efficiently and with increased fuel economy.
Lightweight Structures
Lightweight structures with complex shapes that were previously impossible to achieve using traditional manufacturing methods are now possible. This leads to substantial weight reduction in aircraft components like brackets, brackets, and connectors, which helps improve fuel efficiency and reduce emissions.
Automotive Industry
Customized and Lightweight Parts
Complex components, like intake manifolds, engine brackets, and suspension parts, can be printed with precision, and have the same weight and performance benefits as the aerospace industry. For example, vehicle efficiency, reduced fuel consumption, and improved overall vehicle performance.
Tooling and Prototyping
By 3D printing metal molds, jigs, and fixtures, manufacturers significantly reduce production lead times and costs. This technology makes everything a lot faster and reduces the time required for the development and production processes.
Medical Industry
Implants and Prosthetics
Customized implants, like hip and knee replacements, can be tailored to match a patient’s specific anatomy. The ability to create complex and porous structures with optimized designs allows for better integration with natural bone, improving patient outcomes.
Surgical Instruments
Metal 3D printing is used to manufacture surgical instruments with intricate designs, ergonomic handles, and customized features. This technology enables the production of lightweight, high-performance instruments that enhance surgical precision and reduce fatigue for healthcare professionals.
Dental Applications
Metal 3D printing is also applied in dental applications, such as the production of crowns, bridges, and dental implants. The ability to create detailed and accurate dental restorations using biocompatible metals offers improved aesthetics, better fit, and enhanced patient comfort.
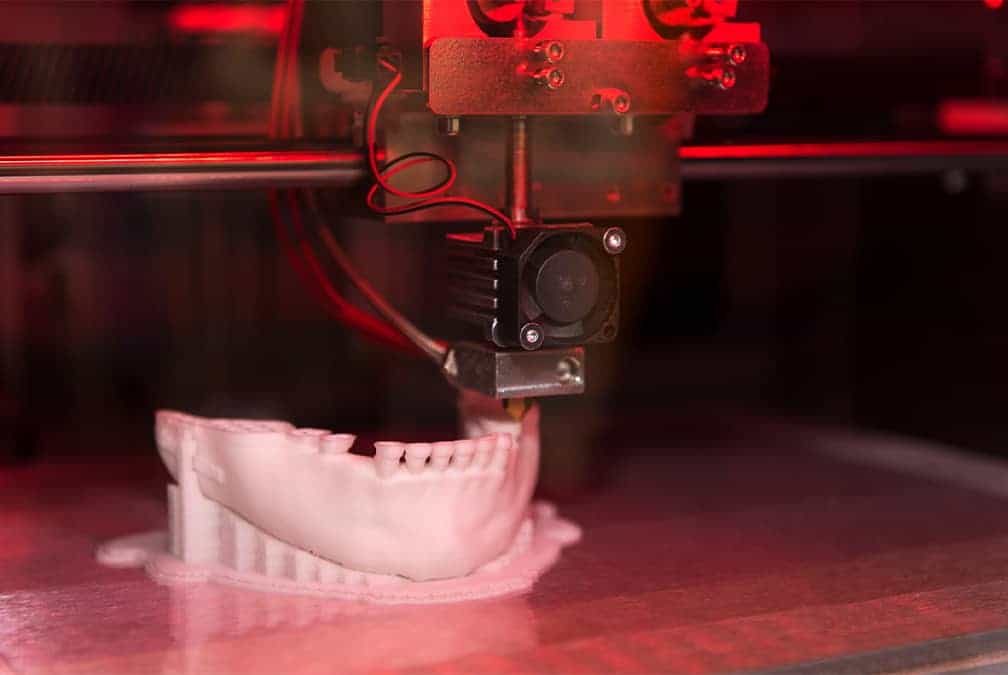
Bioprinting
Bioprinting involves the use of living cells and biomaterials to create three-dimensional structures, such as tissues and organs. It holds great potential in regenerative medicine, drug testing, and personalized healthcare. Advances in bioprinting techniques and bio-inks are enabling more accurate and complex tissue structures to be printed.
Tissue Engineering
Bioprinting is employed in tissue engineering to create three-dimensional structures that mimic the complexity and functionality of native tissues and organs. For example, researchers have successfully bioprinted functional tissues like cardiac patches, skin grafts, and blood vessels. These bioprinted tissues hold potential for regenerative medicine and organ transplantation.
Organ-on-a-Chip Models
Bioprinting is used to create organ-on-a-chip models, which are miniature versions of human organs designed to replicate their physiological functions. These models allow researchers to study disease mechanisms, and test the efficacy of drugs, and personalized medicine. Examples include bioprinted liver-on-a-chip, lung-on-a-chip, and kidney-on-a-chip models.
Drug Testing and Screening
Bioprinted tissues and organ models are utilized for drug testing and screening purposes. By bioprinting specific cell types or tissues associated with a disease or target organ, researchers can study the effects of drugs and test their efficacy and toxicity. This approach provides more accurate and reliable results compared to traditional 2D cell culture methods.
Wound Healing and Skin Regeneration
Bioprinting is used to create skin substitutes for wound healing and skin regeneration applications. By bioprinting layers of living cells, bio-inks, and biomaterials, researchers can produce skin-like structures that facilitate wound healing and tissue regeneration. Bioprinted skin substitutes offer potential solutions for burn victims and patients with chronic wounds.
Bioprinted Organs and Organoids
Researchers are actively working on bioprinting more complex organs, like kidneys, livers, and hearts. While creating fully functional organs is still a challenge, progress has been made in bioprinting organoids—miniature organ structures that mimic certain functionalities. Bioprinted organoids are used for disease modeling, drug testing, and personalized medicine.
Scaffold and Vascular Network Fabrication
Bioprinting is employed to create intricate scaffolds and vascular networks to support tissue growth and organ regeneration. By bioprinting with bio-inks and biomaterials, researchers can construct scaffold structures that mimic the natural extracellular matrix and provide a framework for cell attachment and growth. Bioprinted vascular networks are crucial for ensuring proper nutrient supply and waste removal within bioprinted tissues and organs.
Large-Scale 3D Printing
As 3D printing capabilities continue to improve, there is a growing trend toward large-scale 3D printing. Companies are developing printers with larger build volumes, enabling the production of full-scale architectural prototypes, large industrial parts, and even entire buildings.
Construction and Architecture
Large-scale 3D printing is increasingly being used in construction and architecture. Companies and research institutions have successfully 3D printed entire houses, buildings, and architectural structures. For example, the “Apis Cor” project in Russia used a large-scale 3D printer to construct a house in just 24 hours. Similarly, the “Mars City” project in the United Arab Emirates aims to 3D print an entire city for future Mars colonization.
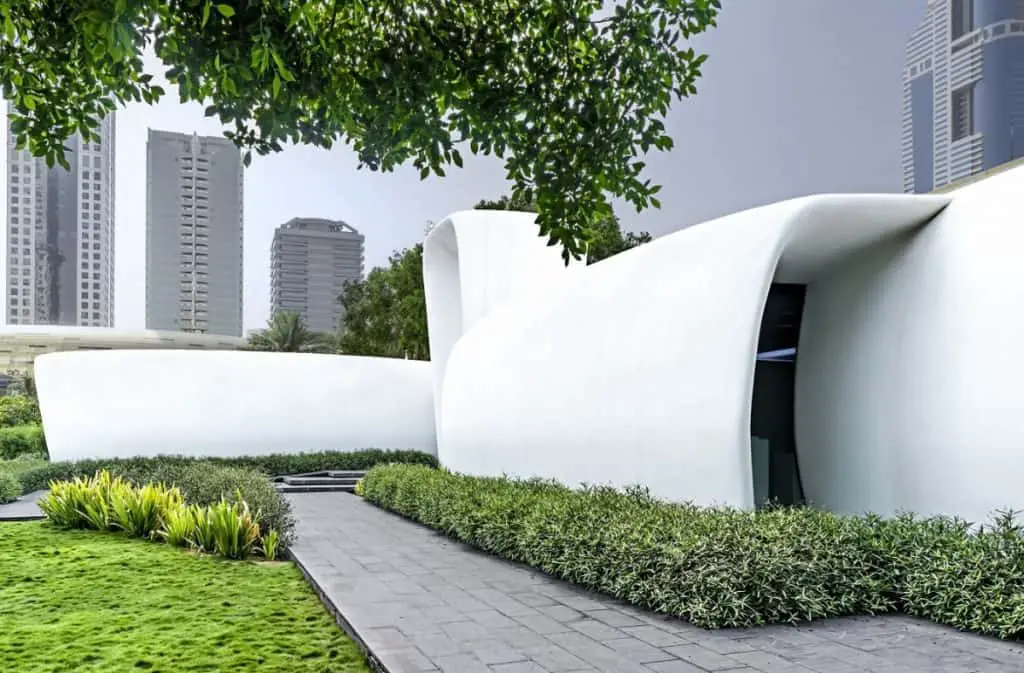
Infrastructure and Bridges
Large-scale 3D printing is also being applied to create infrastructure elements such as bridges and concrete structures. The “Gemini House” project in the Netherlands utilized a large 3D printer to create a pedestrian bridge made of reinforced concrete. The use of 3D printing in bridge construction allows for faster construction, reduced costs, and increased design freedom.
Marine and Offshore Industry
Large-scale 3D printing finds applications in the marine and offshore industry for creating large components like ship parts and oil rig structures. Companies are exploring the use of large 3D printers to manufacture complex and customized parts, reducing lead times and costs associated with traditional manufacturing methods.
Automotive Prototyping
Large-scale 3D printing is utilized in the automotive industry for prototyping large components and vehicle parts. It allows for the rapid production of full-scale prototypes, reducing the time and cost associated with traditional manufacturing processes. This enables manufacturers to iterate designs quickly and test functional prototypes before proceeding to mass production.
Art and Sculpture
Large-scale 3D printing is embraced by artists and sculptors to create large-scale sculptures and art installations. By using large-format 3D printers, artists can bring their creative visions to life on a grand scale, pushing the boundaries of artistic expression and incorporating intricate details and complex geometries into their works.
Aerospace Tooling and Components
Large-scale 3D printing is employed in the aerospace industry for the production of large tooling and components. It enables the manufacturing of lightweight and complex structures, reducing the weight of aircraft and spacecraft and improving fuel efficiency. Large-scale 3D printing also offers the advantage of producing integrated structures that would be challenging or impossible to create using traditional manufacturing methods.
Smart 3D Printing
Smart 3D printers are incorporating advanced sensors and software to optimize the printing process. These printers can detect errors, adjust parameters in real time, and provide feedback on material usage, print quality, and machine performance. Machine learning and AI algorithms are being integrated to enhance the efficiency and accuracy of 3D printing.
Embedded Sensors and Electronics
Smart 3D printing is incorporating embedded sensors and electronics directly into printed objects. This advancement enables the creation of functional and interactive objects with integrated sensors, circuitry, and even wireless connectivity. It opens up possibilities for applications like Internet of Things (IoT) devices, wearable technology, and smart home products.
Self-Healing Materials
Researchers are exploring the integration of self-healing materials into 3D printing. These materials have the ability to repair themselves when damaged or cracked, extending the lifespan and durability of printed objects. Self-healing materials can find applications in various industries, including automotive, aerospace, and consumer goods.
Multi-Material Gradient Printing
Smart 3D printers are now capable of printing objects with intricate multi-material gradients. This advancement allows for the precise control of material properties and characteristics within a single printed object. It opens up opportunities for creating objects with smooth transitions of color, texture, stiffness, and other material properties.
Artificial Intelligence (AI) and Machine Learning Integration
Smart 3D printing is leveraging AI and machine learning algorithms to optimize the printing process and improve object quality. These technologies can analyze and learn from previous print jobs, optimize print settings, and even predict potential issues or failures. This integration enhances efficiency, reduces waste, and ensures consistent and high-quality prints.
Real-Tine Monitoring and Feedback
Smart 3D printers are equipped with sensors and monitoring systems that provide real-time feedback during the printing process. This allows for continuous monitoring of parameters such as temperature, humidity, and print quality. Any deviations or anomalies can be detected and addressed promptly, ensuring better control and quality assurance.
Adaptive Printing and Design Optimization
Smart 3D printers are now capable of adaptive printing, where the printing process can dynamically adjust parameters based on real-time feedback. This enables the printer to adapt to changing conditions and optimize print quality, resulting in more accurate and reliable prints. Additionally, smart algorithms can analyze design files and optimize them for improved strength, weight reduction, or other desired characteristics.
Sustainable Materials and Recycling
There is a growing emphasis on sustainability in 3D printing. Researchers are developing eco-friendly materials, like bio-based plastics and recycled filaments, to reduce the environmental impact. Additionally, efforts are being made to improve the recyclability of printed objects and develop closed-loop systems for material reuse.
Bio-based and Biodegradable Plastics
Researchers are developing bio-based and biodegradable materials for 3D printing, such as polylactic acid (PLA) derived from renewable resources like cornstarch or sugarcane. These materials offer a more sustainable alternative to petroleum-based plastics and have a reduced environmental impact. PLA is biodegradable, meaning it can break down naturally over time, making it suitable for certain applications where disposability is desired.
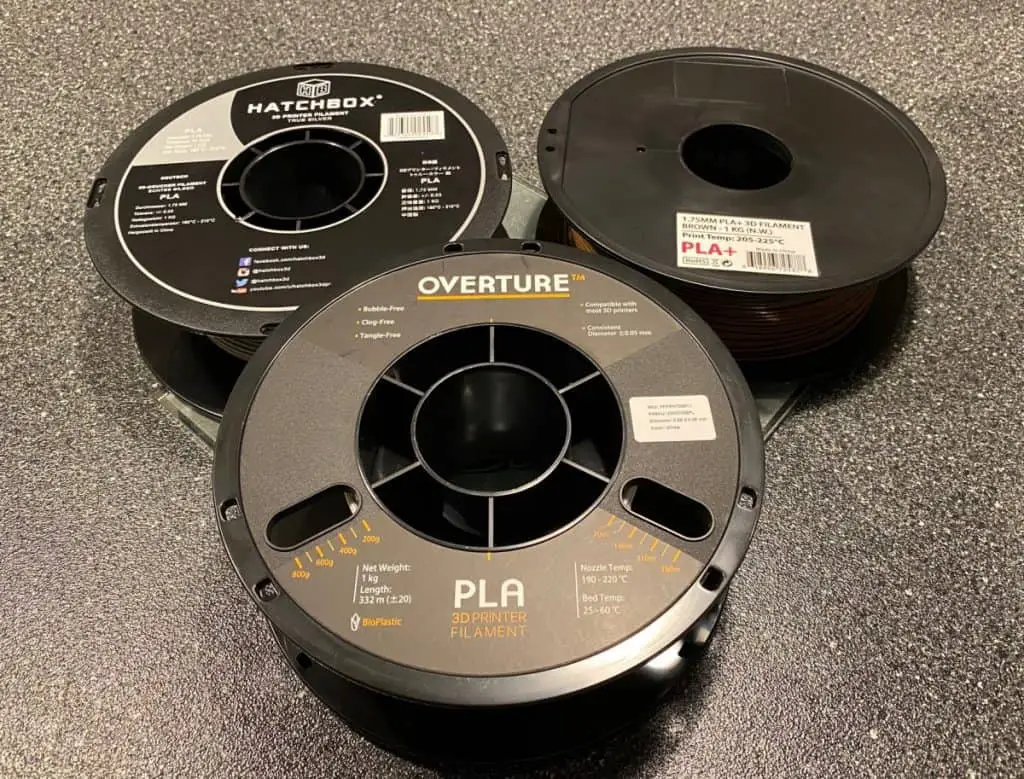
Recycled Filaments
Filament manufacturers are producing 3D printing filaments made from recycled materials. These filaments are typically made from post-consumer or post-industrial waste, like recycled plastics or recycled electronic waste. By using recycled filaments, the 3D printing industry reduces the demand for virgin materials and contributes to a more circular economy.
Closed-Loop Systems
Efforts are underway to develop closed-loop systems for 3D printing, where printed objects can be recycled and reused as feedstock for new prints. This involves collecting discarded prints or failed prints, shredding them into small pieces, and then reprocessing them into a usable filament or raw material. Closed-loop systems promote material reuse, minimize waste generation, and reduce reliance on new material production.
Sustainable Metal Powders
In metal 3D printing, sustainable sourcing and recycling of metal powders are gaining attention. Companies are exploring the use of recycled metal powders, which are produced from scrap metal or post-production waste. By using recycled powders, the environmental impact of mining and refining processes can be reduced, making metal 3D printing more sustainable.
Material Upcycling
Upcycling involves repurposing and transforming waste materials into higher-value products. In 3D printing, upcycling can involve using waste plastic or other materials as feedstock for printing. For example, filament extruders allow users to create their own filaments by melting and extruding plastic waste, turning it into usable printing material.
Design for Sustainability
Another aspect of sustainability in 3D printing is designing objects with sustainability in mind. Designers can optimize their 3D models to reduce material usage, minimize supports, and increase the efficiency of printing processes. Design for sustainability principles ensures that 3D printed objects are resource-efficient, lightweight, and have minimal waste during production.
Hybrid Approaches
Hybrid approaches combine traditional manufacturing techniques with 3D printing. For example, hybrid machines can perform milling, drilling, and other post-processing operations on parts that have already been 3D printed. This reduces the need for separate manufacturing steps and allows for more efficient and cost-effective production.
CNC Machining and Milling
Hybrid machines can combine 3D printing capabilities with CNC machining and milling. After 3D printing a part, the hybrid machine can automatically perform milling or drilling operations on specific areas to remove excess material, create precise features, or achieve surface finishing.
This combination allows for the production of complex parts with higher accuracy and improved surface quality.
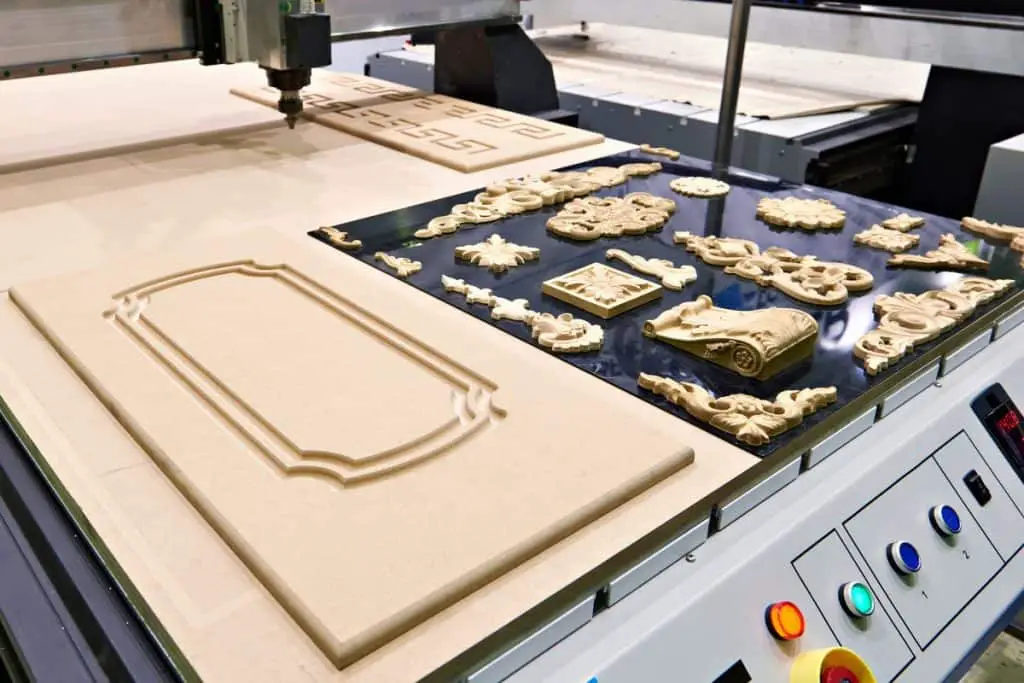
Surface Treatment and Coating
Hybrid approaches can combine 3D printing with post-processing techniques like surface treatment and coating. After printing a part, the hybrid machine can automatically apply coatings, such as protective layers or decorative finishes, to enhance the appearance, durability, or specific functionalities of the printed object. This integration streamlines the manufacturing process and reduces the need for separate coating operations.
Embedding Inserts or Components
Hybrid machines can incorporate traditional manufacturing techniques to embed inserts or components within 3D-printed parts. For example, during the 3D printing process, the machine can pause and insert metal inserts, electrical components, or sensors into specific locations, allowing for the integration of different materials or functionalities into the printed object. This approach combines the advantages of both additive and traditional manufacturing methods.
Post-Processing and Finishing Operations
Hybrid machines can integrate various post-processing and finishing operations with 3D printing. This can include operations like sanding, polishing, painting, or heat treatment. After printing, the hybrid machine can automatically perform these operations, improving the surface quality, aesthetics, or functional properties of the 3D-printed parts. This integration reduces the need for manual post-processing steps and increases efficiency.
Related Articles
- Why Are 3D Printers Getting So Cheap?
- Is It Cheaper to 3D Print D&D Miniatures?
- 3D Printing Actual Costs with Examples
- Will 3d Printing Replace Injection Molding?
- Create a Temperature Tower Using Cura – The Easy Way
In conclusion
3D printing has seen significant advancements across various fields, like aerospace, automotive, and the medical industry. The integration of traditional manufacturing techniques with 3D printing has also opened up new possibilities for efficient and cost-effective production.
Looking ahead, we can anticipate further innovations like improved multi-material capabilities, enhanced bioprinting techniques for complex tissue engineering, and advancements in smart printing with increased automation and AI integration.
The future of 3D printing holds immense potential for how we live in the future.
Make sure you check out our YouTube channel, and if you would like any additional details or have any questions, please leave a comment below or join us on Discord. If you liked this article and want to read others click here.