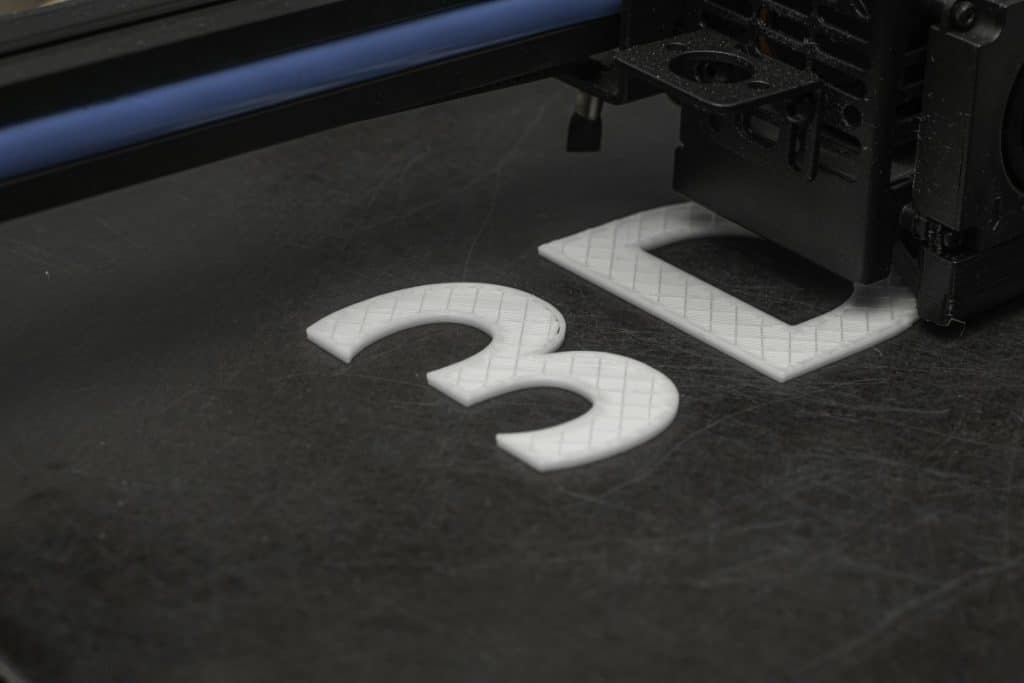
When operating a 3D printer, having a good build plate is vital to making sure that the final product comes outright. In fact, no 3D printer could even work without a proper build plate.
So what is the best 3D build plate? The best build plate for a 3D printer depends on the needs of the printer with regards to price and thermal properties, but the following are some of the best materials for build plates:
- Glass
- Anycubic Ultrabase
- Buildtak FlexPlate
- Easy Peelzy
- Polypropylene
- Geckotek
Finding materials for 3D printer build plates are tricky because they must be secure enough to keep the 3D printed object completely stationary during the print, but they must also allow the 3D printed object to be pulled off the build plate without sustaining damage in the process. Keep reading to find out more about the various materials used to create 3D printer build plates and which ones are the best for you.
Glass
Glass is one of the oldest materials used as build plates in 3D printers and is still arguably one of the most popular given how easy 3D printed objects can be removed from it without damaging the finish of their bottoms. Here are some of the advantages of using glass as a 3D printer build plate:
- Thermal stability
- High modulus of elasticity
- Offers smooth glassy finish to the bottom of 3D objects
- Low conductivity of heat
- Easy to clean after printing operations
- Scratch-resistant surface
There are a few downsides to using glass as a build plate, such as a vulnerability to breakage if the glass sheet is very thin and heated to extreme temperatures. Though only tempered glass is used in 3D printer build plates, even-tempered glass can become strained by exposure to repeated fluctuations in temperature. To avoid this, many 3D printers use ceramic glass, which is significantly more durable.
Anycubic Ultrabase
Anycubic Ultrabase is also a type of glass bed for 3D printers but is a more specialized iteration of the original glass build plates used in 3D printers. Anycubic Ultrabase glass beds are prized by 3D printmakers because they have the ability to secure prints well but are also able to release finished prints easily without damage.
Anycubic Ultrabase is a 3D printer accessory that is manufactured by Anycubic, a Chinese company that specializes in 3D printing technology and has been in operation since 2015. This company has manufacturing bases not only in mainland China but also in the United States and Germany as well.
One of the major advantages of Anycubic Ultrabase build plates is that they are versatile and can support a large number of different thermoplastic materials, including the following:
- PLA
- TPU
- Nylon
- PP
- PETG
- ABS
Like regular glass build plates, Anycubic Ultrabase beds can be easily cleaned between operations using alcohol. One of the drawbacks of the Anycubic Ultrabase as a build plate is that the 3D printed objects on it must be completely cooled in order to be removed from the build plate surface.
Buildtak FlexPlate
The Buildtak FlexPlate is a spring steel build plate that is held to the 3D printer assembly with rare earth magnets. This build plate is best used for batch printing of 3D objects or printing objects with a large base that doesn’t have to be moved around a lot on the 3D printer’s bed.
The Buildtak FlexPlate is intended to be dovetailed for use with other Buildtak 3D printing accessories, but painter’s tape and Kapton can also be used for print adhesion. One of the major advantages of the FlexPlate is its elasticity, which allows 3D printed objects to be popped off of it without having to scrape them off with a tool and risk damage to both the build plate and the 3D print.
Buildtak FlexPlates are easy to use even for those who are just starting out with 3D printing, and these build plates are both versatile and made out of high-quality materials. The downsides to the Buildtak FlexPlate is that they can be expensive and needs to be installed completely flat in order to be effective. This can sometimes be an issue with larger 3D printers which are prone to build plate warping.
Easy Peelzy
Most build plates emphasize adhesion during the 3D print process with easy removal when printing is completed.
When 3D printing first became popular at the beginning of the twenty-first century, the earliest ways of getting a 3D print off the build plate were to scrape it off with a sharp object. Not only did this prove rather dangerous, it also came with the risk of damaging either the 3D print or the print bed.
Easy Peelzy build plates are comprised of two separate sections—the bottom of the build plate (which slots into your existing 3D printer base) and a polymer sticker on the build plate’s surface that allow it to bond with a variety of 3D printing materials.
One of the major benefits of Easy Peelzy is that it can be easily cut to fit the size of any 3D printing surface, allowing it to be customized to a wide variety of 3D printer, but a drawback of this material is that it can’t be used above temperatures of 176 degrees Fahrenheit or it can become demagnetized.
Polypropylene
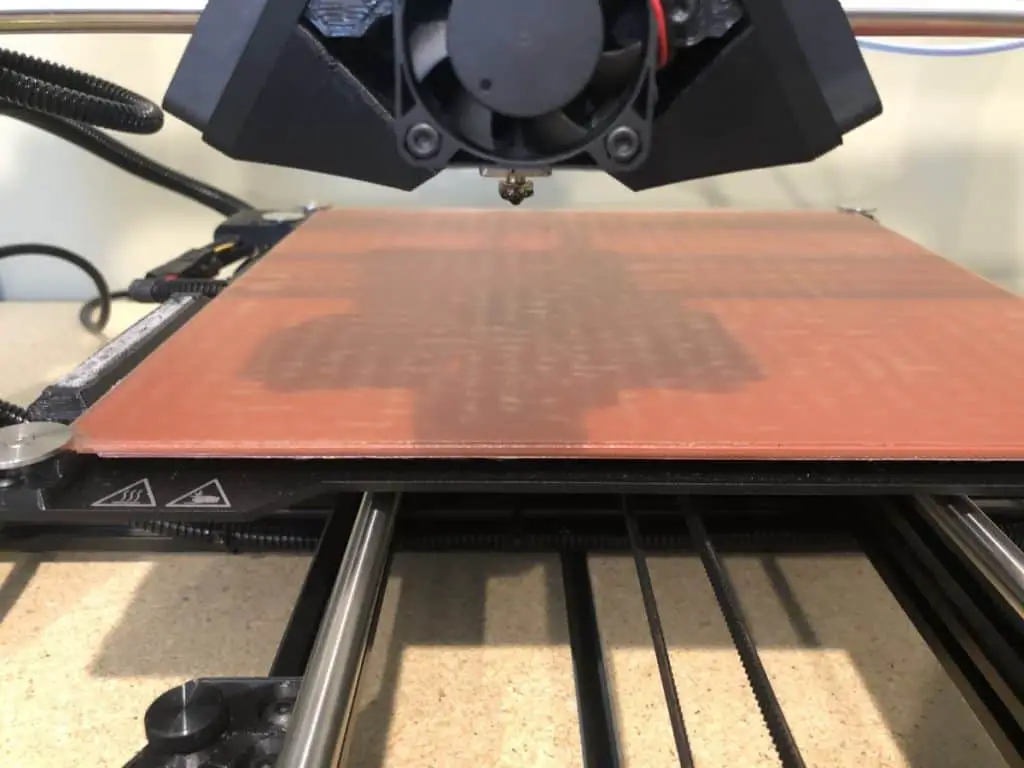
For those 3D printmakers who are looking for a bit of a cheaper solution to the build plate problem, polypropylene sheets can be a very good build plate with similar advantages to more high-tech materials such as the Buildtak FlexPlate, but at a lower price point.
While the cheap price of polypropylene sheets means that they’re an easily replaceable build plate material, this comes with a pretty significant disadvantage, too. Polypropylene sheets are vulnerable to damage during the 3D printing process in the forms of both warping and scratching and aren’t as reliably flat as glass-based build plates.
Polypropylene can also pose some adhesion issues compared to other build plates, but this can be minimized by wiping the build plate down with alcohol between each printing operation. However, a lack of adherence can cause a 3D print build to slide around if the build plate isn’t properly maintained.
Geckotek
Geckotek manufactures build plates that can be applied for either hot or cold 3D printing applications (though there are separate build plates that are designed for each set of printing conditions). These build plates can be used in correlation with any 3D printer and each build plate lasts for over a hundred printing operations before degrading.
Geckotek build plates can be custom cut to any size with nothing more than household or crafting scissors, which makes them a versatile material for 3D print operations. They’re also compatible with the following 3D printing filament materials:
- ABS
- Nylon
- PLA
- PETG
Geckotek building plates take advantage of the most advanced technology that 3D printing has to offer in order to deliver a print bed material that both holds the print securely and also releases it without trouble when the print is done.
3D Printing Build Plate Technology Has Advanced
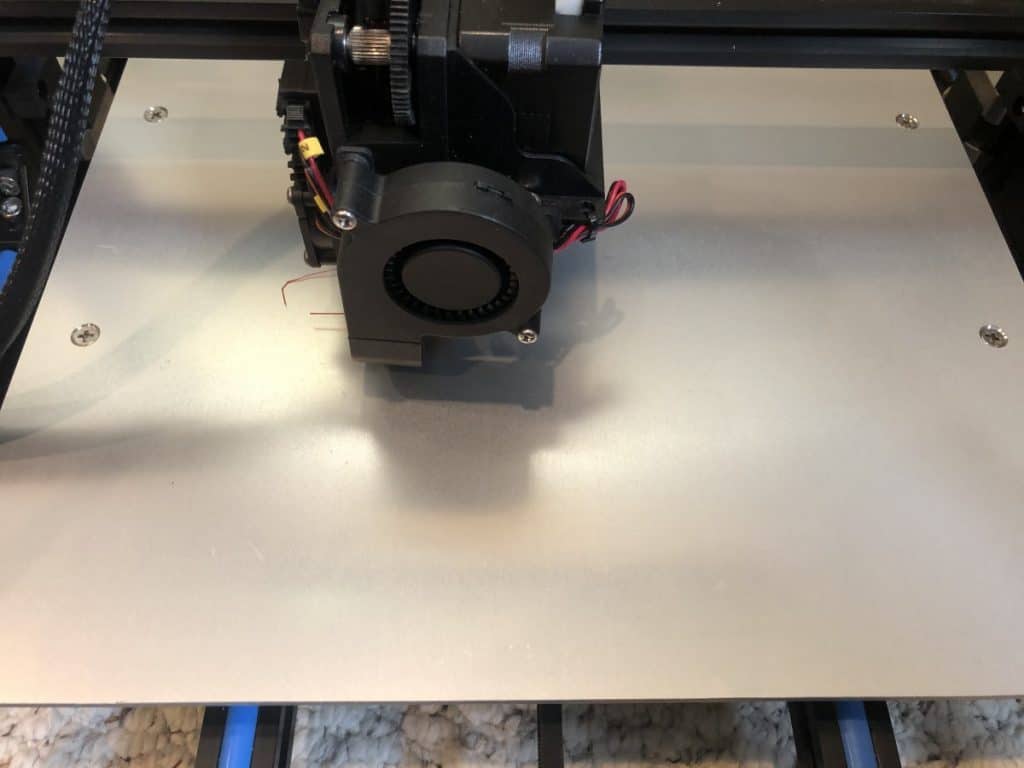
Back when 3D printers were first coming into prominence a decade back, the process was still messy and largely unexplored, leading to build plates and 3D printing materials that were less than ideal.
But now that 3D printing technology has been around for several years, there are many new materials available for build plate construction that make this part of the 3D printing process both more painless and efficient than in previous working models.
Make sure you check out our YouTube channel, and if you would like any additional details or have any questions, please leave a comment below. If you liked this article and want to read others click here.