In the selective laser sintering process, a dynamic laser uses particles of polymer powder, glass, or ceramic to create a three-dimensional model. As your business takes advantage of this astounding technology, you might wonder if the type of laser matters?
When turning digital designs into 3D models, selective laser sintering utilizes a CO2 laser. The CO2 laser works best with the polymer powder since the powder absorbs the laser instead of bouncing off the powder. Another type of laser reflects or bounces off the powder and loses power.
The key to the continued success of selective laser sintering is ensuring the laser delivers the proper amount of energy at just the right time. This article will address how crucial the CO2 laser is for selective laser sintering.
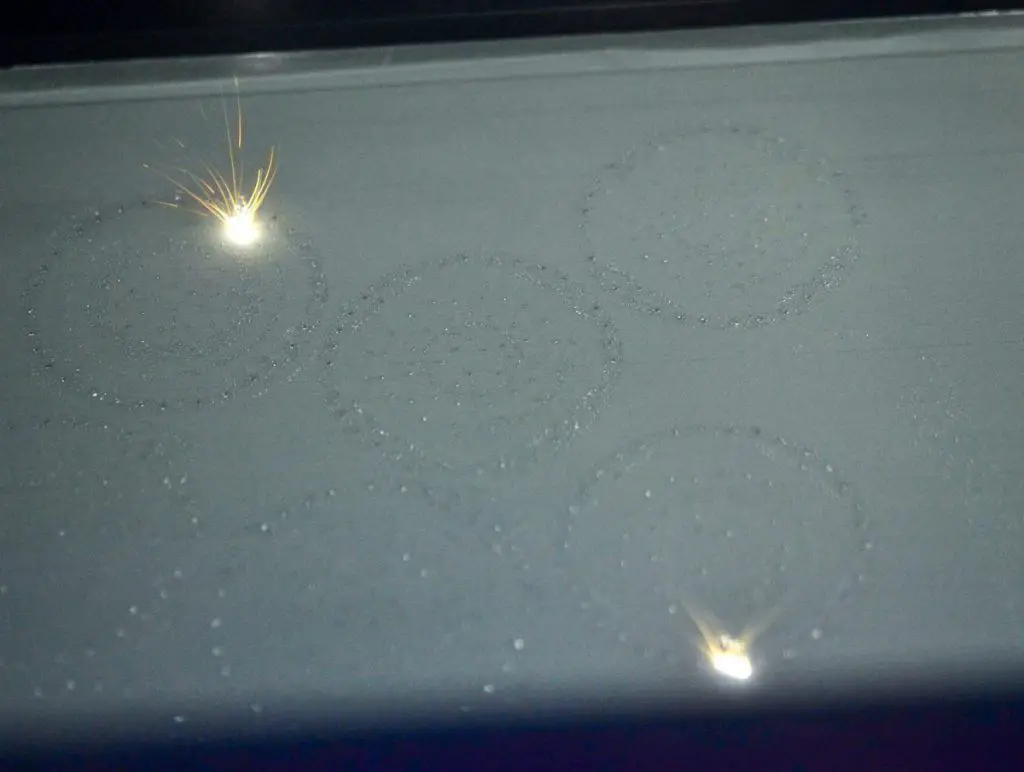
How Selective Laser Sintering Works
Long used in engineering and manufacturing applications, selective laser sintering (SLS) has expanded to myriad uses in medical, custom manufacturing, prototype, and other fields. Understanding the process helps to see where this use of 3D modeling will help your business achieve more.
Selective laser sintering printers utilize the components above. Where a printer differs will be in the size of the build, temperature control, layer deposition, powder dispensing, and model complexity.
The printer must maintain close control of the process to prevent stresses, warping, and heat-produced distortions.
Nylon is the most often used material in selective laser sintering as it produces a stiff, durable complex assembly that stands the test of time well.
Here’s a video to help you envision the 3D modeling operation:
Every part starts as a digital design. The computer tells the laser what to print, and the laser accomplishes the task using high-powered pulses.
SLS printing is the most accelerated additive manufacturing technology to create durable, effective end use parts and prototypes.
Printing
Here are the steps in the printing process:
- Powder within the machine: The specific powder sits on a flat surface inside the printing machine inside the printing machine. The surface heats the powder to just below the melting point.
- Laser scan: The laser scans one part of the 3D model. By heating the particles more, the laser combines the particles into a whole that reflects the model.
- Build chamber: Once one part is complete, the platform lowers to allow the next platform to position at the build process. This happens over and over until the printer finishes the whole model.
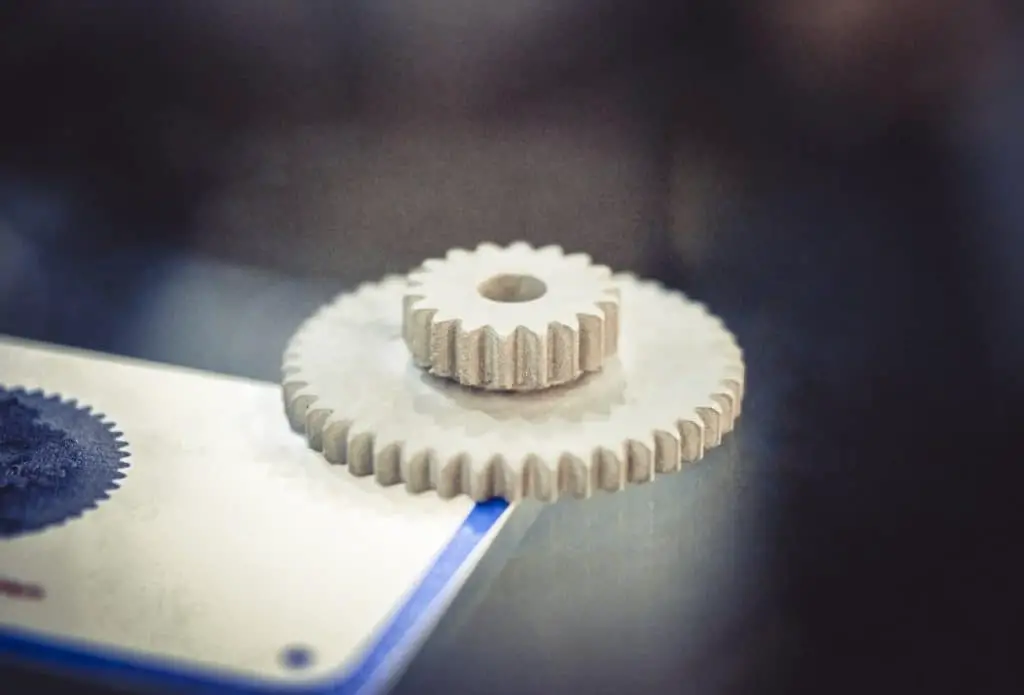
Cooling
The model must remain in the build chamber until it’s cooled. Once the model appears outside the machine, it must cool more until there’s no danger of warping or bending.
Post-Processing
Once they’re outside the build chamber and cooled, you must clean the final parts. The extra powder can go back into the machine for reuse.
Why the CO2 Laser Is Superior
Many manufacturers and businesses prefer the CO2 laser to be in their high-resolution printers for various reasons. These are:
- The CO2 printer is less costly than other printers such as the Ex Fibers.
- The CO2 printer works best with polymer powders.
- The pulsing pattern of this laser allows the powder to absorb the laser.
- The laser doesn’t bounce off the powder, there’s slight power loss.
- The CO2 laser operates at 100% power which reduces the production time.
- You can change the laser beam diameter in the production process.
- The CO2 laser printing machine is ideal for creating a small number of prototypes.
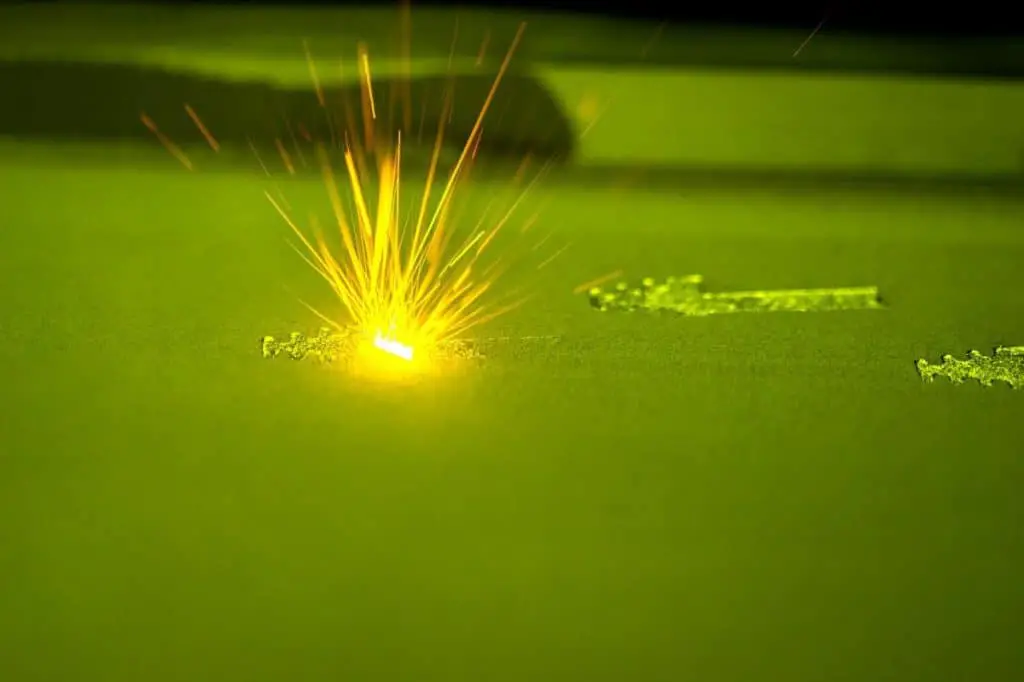
Can You Use Other Lasers for Selective Laser Sintering?
You can use another type of laser other than CO2. The process of selective laser sintering will take longer but still produces a satisfactory model.
- Nd: YAG which stands for neodymium-doped yttrium aluminum garnet: This laser uses an electric current in the form of a laser diode. You’ll find them in oncology centers to remove skin cancer, ophthalmology for cataracts removal, podiatry to treat fungus, and for many applications for dermatology.
- Direct metal laser sintering: Direct metal laser sintering is also known as selective laser sintering. Direct metal laser sintering has many applications in automotive and other manufacturing industries where they need mass production of metal parts. One advantage is that this laser type allows for mixing metal and plastic successfully.
- Er: YAG uses the laser medium erbium-doped yttrium aluminum garnet. The Er:YAG discharges high-energy light to kill diseased cells. This laser is often part of a dermatology practice.
Applications of Selective Laser Sintering
Prosthetics
Historically, when forming a prosthesis, the maker used wax or clay. Selective laser sintering not only speeds the process but produces a very accurate prototype.
Personalized Medicines
The FDA has approved a drug named Spritam for use in humans. Produced entirely using SLS, personalized medicine is free of solvents, has minimal post-processing, and uses polymers approved for such use.
Filters
SLS has the potential for use on borosilicate glass to produce filters for commercial application. This process can vary porosity and density much more quickly than traditional methods.
Bones
SLS produces bones with anatomically solid accuracy. This specific application was to a human temporal bone, but the extension to model other bones accurately exists.
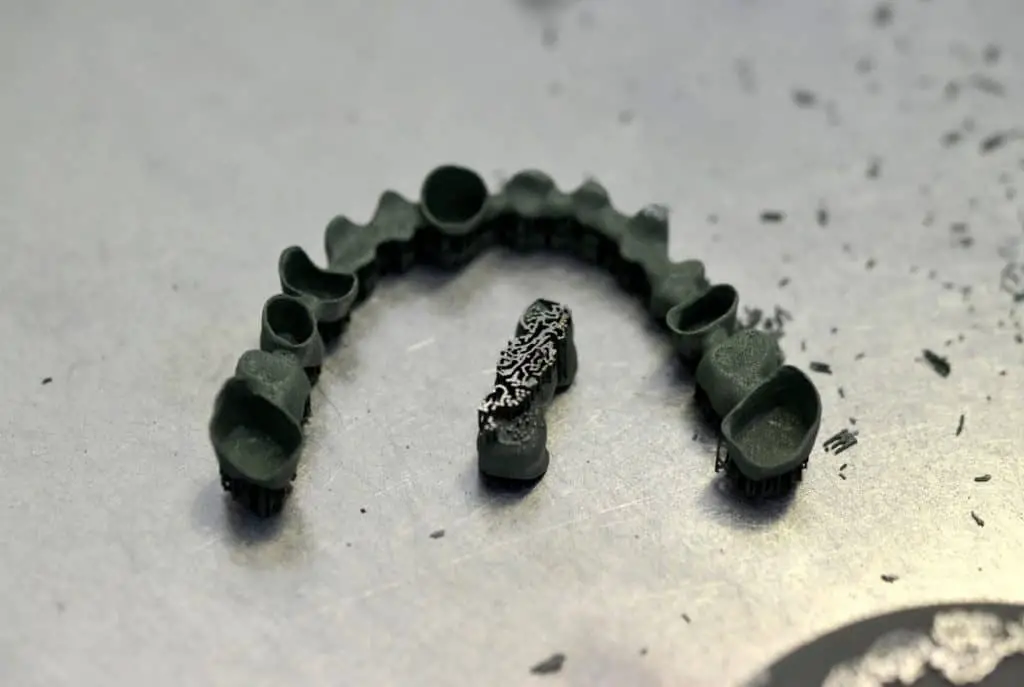
Tissue Engineering
Tissue engineering uses SLS to create temporary three-dimensional scaffolds that guide cell growth. SLS offers an advantage over traditional methods as they can create complicated micro and macrostructures quickly.
Disadvantages of Selective Laser Sintering
The disadvantages to selective laser sintering are the costly machines, cooling sometimes takes as long as printing, and parts have grainy surfaces at times.
Related Articles
Conclusion
While selective laser sintering has been traditionally used in large scale manufacturing contexts, the advent of smaller printers that offer SLS capabilities has expanded the field. SLS offers high productivity, expansive design opportunities, and proven end products.
Outsourcing this process to other companies frequently results in slow lead times and substantial cost. Although an SLS printer is a significant investment, the speed and accuracy with which it produces end products can make the selective laser sintering process worthwhile.
Make sure you check out our YouTube channel, and if you would like any additional details or have any questions, please leave a comment below. If you liked this article and want to read others click here.