Industrial 3D printing is rapidly reshaping the landscape of large-scale manufacturing, offering a range of benefits that traditional manufacturing methods cannot match. From the ability to produce highly customized components to reducing lead times and waste, industrial 3D printers are enabling manufacturers to innovate faster and more efficiently. This article explores the role of industrial 3D printers in empowering large-scale manufacturing projects, the technologies involved, the materials used, and the transformative impact on industries like automotive, aerospace, and healthcare.
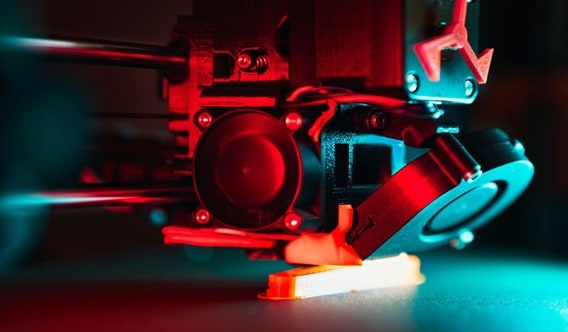
What are industrial 3D printers and how do they work?
Industrial 3D printers are advanced machines designed to produce parts and components at a large scale. Unlike consumer-grade 3D printers, which are used for hobbyist projects or small-scale production, industrial printers are equipped to handle larger build volumes, more complex geometries, and a broader range of materials. The basic working principle behind industrial 3D printing involves adding material layer by layer to create a three-dimensional object based on a digital model.
Industrial 3D printers from Raise3D not only offer superior precision and speed but are also optimized for high-volume production, making them ideal for industries like aerospace, automotive, and healthcare. These advanced machines support a wide variety of high-performance materials, ensuring that even the most demanding applications can be met with durability and accuracy.
Industrial 3D printers typically operate using the following main components:
- Print bed: The surface on which the object is built.
- Extruders: Mechanisms that feed material (plastic, metal, resin) into the printer.
- Filament or material supply: The raw material used to print the object.
- Control systems: Software that translates the digital design into physical form.
- Heating elements and lasers: Used in processes like sintering or melting the material to form the object.
These printers work through additive manufacturing techniques, which involve building parts one layer at a time, allowing for highly precise and customized production.
What are the different types of industrial 3D printers used in manufacturing?
Several types of 3D printing technologies are used in industrial applications, each with its own strengths and limitations. These technologies cater to different manufacturing needs, from producing simple plastic parts to creating complex metal components.
Fused Deposition Modeling (FDM)
Pros:
- Cost-effective
- Widely available
- Suitable for thermoplastics
Cons:
- Lower precision compared to other technologies
- Surface finish often requires post-processing
Typical Applications:
- Prototyping
- Simple components
- Low-cost production
Materials:
- ABS, PLA, Nylon
Stereolithography (SLA)
Pros:
- High precision and smooth surface finish
- Excellent for detailed prototypes
Cons:
- Limited to photopolymer resins
- Expensive materials
Typical Applications:
- Prototyping of intricate parts
- Dental models
- Jewelry design
Materials:
- Photopolymer resins
Selective Laser Sintering (SLS)
Benefits:
- No need for support structures
- Complex geometries can be produced
- Suitable for durable parts
Challenges:
- High cost of materials
- Limited range of available materials
Applications:
- Functional prototypes
- Production of end-use parts
- Aerospace and automotive components
Direct Metal Laser Sintering (DMLS)
DMLS uses a laser to sinter powdered metal, creating strong, dense parts layer by layer.
Pros:
- Excellent for producing metal parts
- High precision
Cons:
- Expensive materials and equipment
- Time-consuming process
Industrial Applications:
- Aerospace engine parts
- Medical implants
- Complex metal structures
Electron Beam Melting (EBM)
How it Works: EBM uses an electron beam to melt metal powder, offering high material strength and excellent density, making it ideal for large-scale metal manufacturing.
Key Advantages:
- Suited for large parts
- Strong, durable metal components
- Used extensively in aerospace and medical implants
How are industrial 3D printers empowering large-scale manufacturing projects?
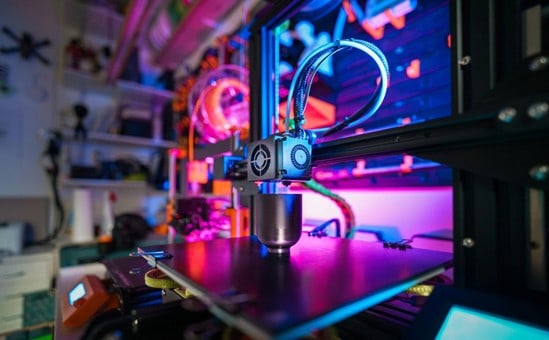
Industrial 3D printing has introduced a host of transformative benefits to large-scale manufacturing, enabling faster, more flexible production and more innovative design possibilities. Below are some of the key advantages:
- Reduced lead times: 3D printing accelerates the design-to-production process.
- Customization: It allows manufacturers to create custom parts tailored to specific needs without retooling.
- Prototyping speed: Rapid prototyping capabilities streamline the development phase.
- Cost efficiency: Less waste and reduced need for expensive molds or tooling.
How does 3D printing enable faster prototyping in manufacturing?
One of the key advantages of industrial 3D printing is the ability to create rapid prototypes. This significantly shortens the product development cycle, allowing designers to quickly iterate on designs, test prototypes, and make adjustments without the lengthy wait times associated with traditional manufacturing processes. Prototypes can be produced in a matter of hours or days, compared to weeks or months using conventional methods.
What are the benefits of 3D printing for mass customization?
Mass customization is another area where industrial 3D printing shines. Manufacturers can produce unique or customized parts without the need for tooling changes or expensive setups. This allows businesses to offer personalized products at a mass scale, from custom-fit medical devices to tailored automotive components, enhancing customer satisfaction and driving innovation.
How does 3D printing reduce waste in manufacturing?
Industrial 3D printing is also known for its efficiency in reducing material waste. Traditional subtractive manufacturing techniques (such as milling or cutting) often result in significant waste, as materials are cut away from larger blocks. In contrast, additive manufacturing only uses the material necessary to create the part, minimizing waste and reducing costs. Here’s how:
- Material efficiency: Less material is wasted during the production process.
- Reduced tooling: No need for specialized tooling that generates excess waste.
- Precision: Exact material usage ensures efficient production.
What materials are used in industrial 3D printing for large-scale manufacturing?
Industrial 3D printers are capable of using a wide variety of materials, making them versatile for different manufacturing needs. Here are some of the common materials:
- Thermoplastics: ABS, PLA, Nylon
- Metals: Stainless steel, Titanium, Aluminum
- Resins: Photopolymers for precise models and prototypes
What are the most common plastics used in industrial 3D printing?
Plastics like ABS, PLA, and Nylon are frequently used in 3D printing, each offering different manufacturing properties. ABS is known for its durability, PLA for its ease of use and biodegradability, and Nylon for its flexibility and strength.
What metals can be 3D printed for industrial applications?
In metal 3D printing, materials like Stainless Steel, Titanium, and Aluminum are commonly used for their strength and lightweight properties. These materials are ideal for industries such as aerospace and automotive, where weight and durability are critical factors.
What advanced materials are emerging in industrial 3D printing?
Emerging materials such as composite resins and biocompatible materials are opening new possibilities in fields like medical device manufacturing and construction. These advanced materials allow for more complex and durable products to be made, pushing the boundaries of what 3D printing can achieve.
How does 3D printing affect the cost structure of large-scale manufacturing?
Industrial 3D printing can significantly impact the cost structure of manufacturing by reducing material waste, minimizing tooling expenses, and speeding up production cycles. While the upfront cost of industrial 3D printers can be high, the long-term cost savings can make them a valuable investment for large-scale manufacturers.
What are the cost benefits of industrial 3D printing?
The cost benefits of industrial 3D printing are extensive, especially when considering the full product lifecycle. Here are some key cost-saving factors:
- Lower material waste: Additive manufacturing only uses the material required for the part, leading to minimal excess material.
- Reduced need for molds and tooling: Traditional manufacturing often requires expensive molds or tools, which are not necessary in 3D printing.
- Faster production cycles: With 3D printing, parts can be created more quickly, which reduces lead times and increases efficiency.
- On-demand production: Manufacturers can produce parts as needed, reducing inventory costs and the risks of overproduction.
What are the challenges and limitations of 3D printing in large-scale manufacturing?
Despite its many advantages, 3D printing in large-scale manufacturing does come with certain limitations:
- Higher material costs: While 3D printing reduces waste, the cost of raw materials (especially metals) can be higher than traditional materials.
- Machine maintenance: Industrial 3D printers require regular maintenance, which can add to operational costs.
- Speed limitations: Depending on the technology, 3D printing may still be slower compared to traditional mass production methods, particularly for high-volume orders.
What are the main industries using industrial 3D printing for large-scale manufacturing?
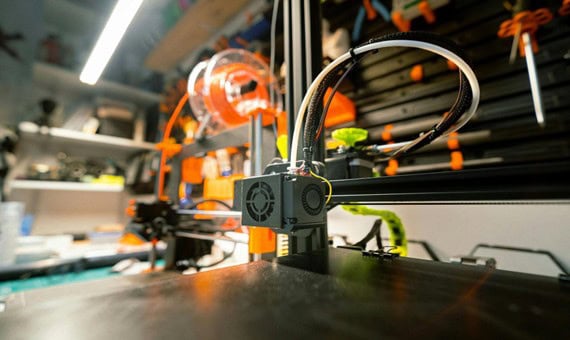
Industrial 3D printing has been adopted across several key industries, each leveraging the technology to solve unique challenges and drive innovation. Here are a few examples:
- Automotive: Used for rapid prototyping, lightweight components, and custom parts.
- Aerospace: Ideal for producing complex, weight-efficient parts that reduce overall aircraft weight.
- Healthcare: Enables the production of custom prosthetics, implants, and medical tools tailored to individual patients.
- Construction: Allows for the creation of unique architectural components and on-site manufacturing.
- Consumer Goods: Facilitates mass customization, allowing manufacturers to produce personalized products at scale.
How is the automotive industry using 3D printing?
In the automotive industry, 3D printing is used for rapid prototyping, enabling designers and engineers to iterate on new designs quickly. Additionally, lightweight components produced through additive manufacturing help improve fuel efficiency in vehicles by reducing their overall weight.
How is 3D printing transforming aerospace manufacturing?
Aerospace manufacturers use 3D printing to create complex parts that would be difficult or impossible to produce using traditional methods. The weight reduction achieved through 3D printing is a significant advantage, as it helps improve fuel efficiency and overall performance in aircraft and spacecraft.
What role does 3D printing play in healthcare and medical device manufacturing?
In healthcare, 3D printing enables the production of custom prosthetics, implants, and medical tools. Because these items can be tailored to the individual patient, they offer better fit, function, and outcomes. Additionally, 3D printing is being explored for bio-printing applications, such as printing tissues or even organs.
How to choose the right industrial 3D printer for large-scale manufacturing?
Choosing the right industrial 3D printer for large-scale manufacturing requires careful consideration of several factors, including material compatibility, build volume, and precision. The following guide can help manufacturers select the right printer for their needs.
What are the key features to look for in an industrial 3D printer?
When evaluating an industrial 3D printer, consider these key features:
- Build size: Ensure the printer can accommodate the size of the parts you intend to produce.
- Layer resolution: Higher resolution printers can produce more detailed and precise parts.
- Material range: Look for printers that support the materials you need, whether they are plastics, metals, or resins.
- Post-processing requirements: Some printing technologies require additional steps, such as cleaning, curing, or polishing, which can add time and cost.
What are the most important questions to ask when evaluating a 3D printer?
Before purchasing a 3D printer, manufacturers should ask the following questions:
- What is the expected output volume?
- What are the maintenance needs of the printer?
- What is the total cost of ownership, including materials and maintenance?
- How will the printer integrate with existing manufacturing workflows?
- What level of post-processing is required?
What are the advantages and disadvantages of 3D printing in large-scale manufacturing?
Like any technology, industrial 3D printing comes with its own set of advantages and disadvantages, particularly when it comes to large-scale production.
What are the main advantages of 3D printing in manufacturing?
Here are some of the key advantages of 3D printing in large-scale manufacturing:
- Flexibility: Can produce complex geometries that are impossible with traditional methods.
- Waste reduction: Uses only the necessary material, minimizing waste.
- Faster prototyping: Reduces time to market with rapid prototyping.
- Customization: Allows for personalized products without major retooling or setup changes.
- On-demand production: Reduces the need for large inventories.
What are the disadvantages of 3D printing for industrial production?
However, there are also some challenges associated with 3D printing at an industrial scale:
- Speed limitations: While ideal for prototyping, 3D printing can be slower than traditional manufacturing for mass production.
- Material restrictions: Some materials may not be suitable for 3D printing or may require expensive modifications.
- High equipment costs: Industrial 3D printers can be expensive to purchase and maintain, especially for smaller manufacturers.
- Post-processing requirements: Depending on the technology, additional post-processing steps may be needed to achieve the desired finish or functionality.
What are the best practices for integrating industrial 3D printing into large-scale manufacturing workflows?
To get the most out of 3D printing, manufacturers must consider how to effectively integrate it into their existing workflows. Below are some best practices:
- Provide thorough training: Ensure that staff is trained on both the operation of the 3D printers and the necessary design software.
- Leverage hybrid manufacturing: Combine 3D printing with traditional methods to maximize efficiency and quality.
- Automate where possible: Integrating automation can improve both speed and consistency in production.
How can companies combine 3D printing with traditional manufacturing methods?
Hybrid manufacturing is an approach where 3D printing is combined with conventional methods, such as CNC machining. For example, companies can 3D print complex internal structures and then use machining to create smooth outer surfaces. This allows manufacturers to leverage the strengths of both technologies, combining precision and scalability.
How to ensure quality control in 3D printed parts for large-scale projects?
Ensuring the quality of 3D printed parts requires a combination of good design practices, material verification, and post-processing steps. Some best practices include:
- Testing: Conduct regular testing to ensure parts meet strength, durability, and accuracy requirements.
- Material verification: Verify the consistency and quality of the materials used.
- Post-processing: Implement proper post-processing techniques, such as heat treatments or surface finishing, to improve the final product.
Conclusion
Industrial 3D printing is revolutionizing large-scale manufacturing, offering unparalleled flexibility, customization, and efficiency. As manufacturers continue to integrate 3D printing into their workflows, they are discovering new ways to reduce costs, improve product quality, and accelerate innovation. From rapid prototyping to mass customization and hybrid manufacturing, 3D printing is poised to become a cornerstone of modern manufacturing. Understanding the different technologies, materials, and best practices will be key for any company looking to stay competitive in this evolving landscape.